Tools & Resources
Jack Pesch Bridge
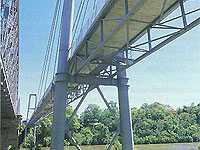
Jack Pesch Bicycle and Pedestrian Bridge which spans the Brisbane River. The concrete deck is supported by, and acts compositely with, two fully welded steel trusses made from Grade 350 XLERCOIL® RHS sections.
Location: | Brisbane, Queensland |
Country: | Australia |
Construction Date: | October 1998 |
Products Used: |
AS/NZS 1594 - HA350 XLERCOIL® |
Awards: | High Commendation - The Institution of Engineers, Australia (Queensland Division)Engineerig Excellence Awards 1999. High Commendation - Australian Institute of Steel Construction, Structural Engineering Steel Design Awards 1999. |
The award winning Jack Pesch Bicycle and Pedestrian Bridge which spans the Brisbane River, employed an elegant clear span, low cost design solution which blends modern technology with the style of two nearby heritage listed bridges. The three span cable stayed structure is a showpiece of alternative design in structural steel, costing 15% less than a design conforming to tender, while still meeting all design and functional criteria.
With its 167 metre single span across the river, two piers originally planned to stand in the river were eliminated. Just one of the several features for which the bridge was highly commended in Institution of Engineers, Australia and AISC awards. The judges were also impressed by the engineering analysis undertaken to ensure pedestrian comfort and the efficient use of structural steel in the form of a two metre deep truss, instead of plate girders.
The Jack Pesch Bicycle and Pedestrian Bridge spans the Brisbane River between Indooroopilly and Chelmer and was funded jointly by the Queensland Department of Main Roads and Brisbane City Council. Moggill Constructions Pty Ltd built it to a design by Kinhill Pty Ltd for A$2.73 million, some 15 percent below the conforming tender cost of A$3.24 million.
A major challenge for the design was to blend in with two nearby rail bridges which are heritage listed.
The Albert Bridge, a steel truss structure of two 104 metre spans, constructed in 1898, while the Walter Taylor Bridge was built in 1936 as a toll bridge.
Although the Jack Pesch Bridge echoes the character of its neighbours, its construction is thoroughly modern. Its two 41 metre high towers comprise twin 1.2 metre diameter steel tube columns braced together, with the tower tops anchored to the underlying rock with Freyssinet permanent rock anchors. The four metre wide deck (with a navigable clearance of 13 metres) is supported from the top of the towers by a plane of cables at 19 metre intervals along each side.
A key feature is the Austress Freyssinet multi-strand cable support system, comprising polyethylene sheathed multi-strand 15.2 milimetre strands enclosed in high density polyethylene protective casings. Each cable contains up to 55 such strands, and the Austress "Isotension" system allows tensioning of each strand consecutively with lightweight stressing equipment so that all strands have identical tension.
The concrete deck is supported by, and acts compositely with, two fully welded steel trusses made from Grade 350 XLERCOIL®* RHS sections. Trusses are spaced 3.9 metres apart, while the deck consists of precast concrete slabs in 2.5 metre widths spanning between the two trusses.
All steel reinforcement was supplied by OneSteel.
Engineering
Kinhill principal structural engineer, Ken Ross, said the high strength-to-weight ratio of structural steel and the relatively light loads to be supported made steel the obvious design choice.
He said the steel truss design offered improved dynamic performance in addition to eliminating the river piers, achieving the desired aesthetics and reducing the cost."The most critical aspect of a relatively light pedestrian bridge is its dynamic performance, which needs to ensure the comfort of the pedestrians, and allay concerns about the safety of the bridge," he said. In addition to following the Australian Bridge Code and the Australian Wind Code, Kinhill researched the available technical literature to ensure its design improved on the dynamic performance of the original.
Kinhill conducted a three-dimensional modal analysis and compared the dynamic performance of the two designs with limits recommended by A.W. Irwin in Human Response to Dynamic Motion of Structures (The Structural Engineer, No. 9, 1978). The bridge comfortably met Irwin's criteria for vertical motion. Under wind load, where the lateral accelerations increase as the wind speed increases, the alternative design performed approximately twice as well.
Moggill Constructions project manager Frank Sturley said the light weight of steel contributed greatly to the ease of construction. He said this allowed for a simple process of erecting 10 tonne deck truss segments using a lightweight lifting frame, and securing each truss segment in turn with cables.Construction
Work began on the Chelmer side, where the abutment and tower were constructed before the process was repeated on the Indooroopilly side. Next, 19 metre cantilevered truss sections were lifted from a barge, utilising a heavy duty tow truck winching from the embankment. Working from the Chelmer side first, the cantilevered trusses were supported by initial cable strands. Once the closure truss was lifted between the two opposing cantilevered deck ends, the Chelmer deck was jacked towards the Indooroopilly deck and the closure butt welded.
With the completed trusses in place, the precast concrete deck units were erected, the in situ concrete kerbs cast, and the deck furniture added.
Importantly, each stage of the bridge erection was structurally analysed to determine the cable forces and deflected profiles resulting from that stage. When each strand was introduced to the cable, it was locked into the structure to achieve a level (or slightly cambered) deck profile when all the dead load was applied. After each stage where cables were introduced, the actual cable forces and deflected shape were compared to predetermined data, and adjustments made to subsequent stages as necessary. In all, there were 80 stages.
Fabrication
Sun Engineering Pty Ltd fabricated the 14 truss sections and two tower frames in its workshop at Carole Park. In order for the bridge deck to be level when complete, the trusses were fabricated with an upward camber, achieved by a series of angle changes at the splices between straight truss segments. Further, since the tower legs are inclined to the plane of the cables, setout of the tower head and cable anchorages was required in three dimensions, achieved through sequential assembly.
The accuracy of fabrication, and in particular the successful cambering of deck trusses and accurate fabrication of the tower heads and cable anchorages, ensured that only very minor rectification was required on site. Total steel weight in the bridge is 230 tonnes, of which the deck is 138 tonnes, and the towers are 92 tonnes. The tower frames, which extend 22 metres above deck level, are painted in "St Enoch's Grey", as approved by the Heritage Council.
Maintenance
A special attraction of this bridge is the provision made for maintenance. For example, the cable system allows each strand, within its cable, to be individually replaced, and in turn each cable can be replaced separately while the bridge is in use. Further maintenance convenience is designed into the structural steel. Internal access is available inside the pier towers via a vertical ladder with a Fallright safety system, and an under slung maintenance trolley can run the full length of the bridge for easy access to all surfaces under the deck .
* From 1 August 2002, BlueScope Steel Plate Products are known as XLERCOIL®